Various position control modules from simple versions for
analog sensors up to axis control modules with fieldbus coupling.
Highlights are the POS-321-P and UHC-126-U-*.
Application information (used in some of our positioning control modules):
Compensation of static positioning errors
Using PT1 or P control function
High accurate and robust syncronisation control
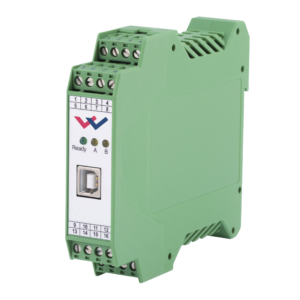
POS-123
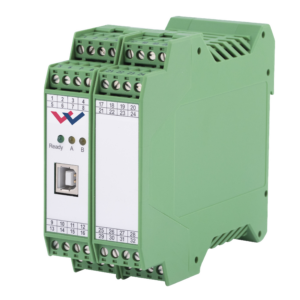
Universal positioning module, optionally with power output stage or SSI interface
Typical applications:
- general positioning drives
- fast transport drives
- handling systems and
- speed-controlled axes
read more
This electronic module has been developed for controlling hydraulic positioning drives. Proportional valves with integrated or external electronics can be controlled with the universal analog output.
The internal profile generation is optimized for stroke-dependent deceleration or the NC control mode. The controller and the controller settings are adapted to typical requirements and thus permit rapid and uncritical optimization of the control behavior. The optimized control function offers a high degree of precision together with high stability for hydraulic drives. The movement cycle is controlled via the external position and speed inputs; in SDD mode as a particularly robust and easy-to-parameterize control and in NC mode via the internal profile generator.
Alternatively, the P version is available with an integrated power output stage. The advantage of the integrated power output stage is founded in the integrated control behavior without additional dead times. This allows higher dynamics respectively a higher stability.
New to our family of hydraulic axis positioners is now a module with integrated power stage and Profinet interface. This combination allows cost-effective and robust proportional valves to be used without internal electronics.
The SSI extension is available for use with digital sensors . Sensors with a resolution of one µm can be used for very high position accuracy.
POS-123-U-P-SSI
POS-123-P-PFN
POS-123-P-PFN PLC Block
GSDML-file SIMATIC driver
POS-321-P
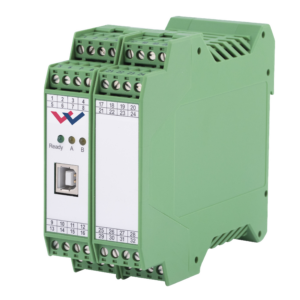
Digital positioning unit with integrated commissioning assistant and flexible script programming option
Advantages:
- In addition to the basic function, individual controls can be realised
- This provides numerous application possibilities, even without an external PLC
- Assistance system as commissioning aid
- Only basic data must be provided
- Time saving until the axis is ready to run
- Robust system behaviour without having to parameterise the controller itself
read more
The basis of this unit is the standard positioning module POS-123.
This is extended here by two interesting additional functions:
The FlexiMod script programming allows the basic function of the module to be individually supplemented and adapted by means of simple commands. This enables the realisation of interesting additional functions such as setpoint control, oscillating functions, special monitoring, parameter control, etc.
Script-based programming is much easier to handle than a PLC programming language and allows typical requirements to be realised in the most compact way. Since it is used here in addition to the predefined positioning algorithm, the assembly can also be operated as a conventional positioning module without using this option. The script only includes the desired extensions, so that the effort for adaptation is minimal. All script commands are processed in a fast cycle of 1 ms.
The assistance system, which is also integrated, serves to simplify the commissioning of hydraulic positioning controls. The analysis and automatic setting of various parameters should help the user to parameterise the control module more quickly. The aim of this automatic parameterisation is to obtain an executable system with robust behaviour as quickly and easily as possible.
The commissioning assistant offers various functions that can be used individually, in combination or as a complete package. These include determining and parameterising the sensor range, the polarity and offset. When using a controller with integrated power output stage, mostly positively overlapped proportional valves are controlled. In order to achieve a stable control behaviour, this overlapping must be measured and compensated. This is also accomplished by the assistant here. Furthermore, the position controller’s gain will be parameterised on the basis of dynamic measurements.
POS-321-P
Additional manual for integrated simulation
POS-323-P
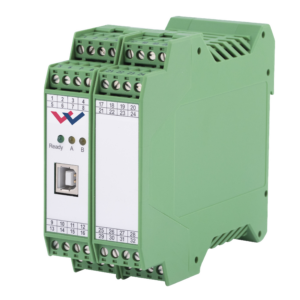
Digital positioning control unit with integrated automatic commissioning assistant
Automatic functions:
- sensor scaling
- deadband compensation (in case of overlapped valves)
- zero point adjustment (in case of zero overlapped valves)
- measuring of the maximum speed for each direction
- measuring of the response of the system to set the closed loop control parameter
read more
Basis of this device is the standard positioning controller POS-123. The integrated commissioning assistant was made for an easier start-up of a hydraulic positioning control. Analyzing and automatic parameterizing of several settings should help the user to adjust the system in a shorter time. Intention of this functionality is getting a system ready to work in a stable way as quick and easy as possible.
The assistant provides different functions, which can be executed separately, combined or in complete scope of operation. Among those functions are detecting and parameterizing the usable working stroke, the polarity and a possible offset, as well as a deadband of the valve and the usable maximum speed. By means of a dynamic investigation, furthermore the control parameters can be set. The functional range of the assistant system differs between U and P version of the controller because different kind of valves are controlled with these modules.
POS-323-P
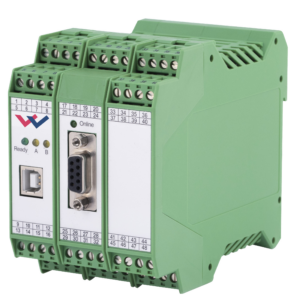
POS-124-U
Two-axis positioning and synchronization control module with
integrated ProfiNet IO resp. Profibus DP interface and SSI sensor interface
Typical applications:
- position control and/or
- synchronization control with hydraulic axes
read more
This electronic module has been developed for controlling two hydraulic positioning axes.
Both axes can be driven independently or controlled in synchronous mode via ProfiNet / Profibus / EtherCAT.
The differential outputs are provided for the control of proportional valves with integrated or external electronics (with differential input). Alternatively, the output can be parameterized to 4… 20 mA. This module is designed for the use with analog position sensors 0… 10 V or 4… 20 mA (scalable) as well as digital SSI sensors.
The internal status and faults information are transmitted to the master controller. Additionally, the operational readiness is reported via a READY output.
UHC-126-U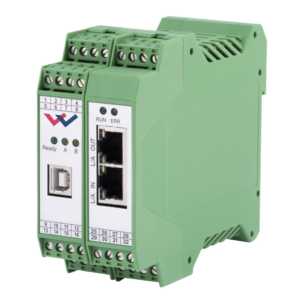
Axis control module with universal positioning, pressure limitation control and fieldbus interface, available with EtherCAT, Profinet or Profibus interface
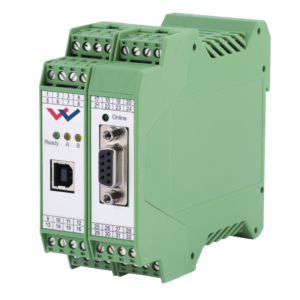
Typical applications:
- positioning drives
- fast transport drives
- handling axes
- forming machines with position and pressure control as well as feed drives
- linearized hydraulic system by the MR-controller
read more
This electronic module was developed for controlling hydraulic axes via an integrated fieldbus interface. The hydraulic axis can be driven as positioning control with digital stroke measuring (SSI interface) or by an analog sensor.
In addition, a force or differential pressure control is implemented. This can be used autonomously or as a pressure-limiting control.
Command values and control signals are transmitted to the module by fieldbus. Feedback are status information and actual values. The differential output is designed for the control of proportional valves with integrated or external electronics (differential input). Alternatively, a 4 … 20 mA current signal can also be parameterized. Internally the system is monitored for several failures and states. The READY message is available as a fieldbus signal and digital output.
The parameterization is realized via an USB interface in combination with our PC program WPC-300 with integrated oscilloscope function. Alternatively, defined parameters can be modified via the ProfiNet interface.
PPC-125-U-PDP
Universal axis controller with Profibus, position control, pressure control and SSI interface
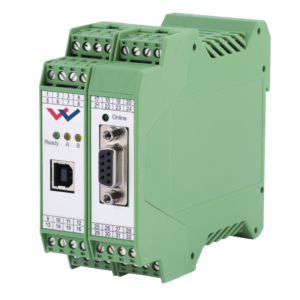
Typical applications:
- positioning drives
- fast transport drives
- handling axes
- forming machines with position and pressure control as well as feed drives
read more
This electronic module was created to control hydraulic axes by an integrated Profibus DP interface. The hydraulic axis can be driven as positioning control with digital stroke measuring by a universal SSI interface or an analog sensor.
In addition, a force or differential pressure control, which operates autonomously or as a pressure-limiting control function, is implemented.
Command signals and actual values are transmitted by a Profibus communication interface. Feedback are status information and actual values.
Parameterization is possible by our PC program WPC-300 with integrated oscilloscope function. Alternatively, defined parameters can also be adjusted via the Profibus interface.
PPC-125-U-PDP
GSD File