From bypass control to multi-axis synchronizing and positioning control with Profibus and CAN Bus, we offer a complete range of solutions for a wide range of applications
CSC-158-U-SSIC
Axis control system with synchronisation function, pressure limiting control,
SSI sensor interfaces and Profinet connection
Typical applications:
- Positioning
- Synchronization control
- Pressure/force limitation control
This system is a positioning control system with options for superimposed synchronization control and force or pressure limiting control of the individual axes.
Up to 4 axes can be controlled via the field bus.
- Positioning: As with our standard positioning controller, an axis can be operated as point-to-point control (stroke depended deceleration) and in NC mode (speed-controlled). The controller is optimized based on a few parameters; the motion profile is specified via the fieldbus (position and speed). The axes can be operated together or with individual setpoints.
- Synchronization control: If several axes are operated, a superimposed synchronization controller can be activated. A PI or PT1 controller is available as the control structure.
Depending on the system requirements, both the master-slave concept and averaging (control of all axes to an internally calculated setpoint position depending on the individual positions and the setpoint position) are available. - Pressure/force limitation control: The force can be measured and limited via one or two pressure sensors. If the system switches from synchronization control to pressure/force control, this then has priority and replaces position control.
UHC-126-U-S2
Axis control module with universal positioning, pressure limitation control and Fieldbus interface, special version for distributed synchronization control
Typical applications:
- general positioning drives
- fast transport drives
- handling systems
- speed-controlled axes
- presses with positioning and pressure control
This electronic module was developed for controlling the position and/or pressure of a hydraulic axis via the integrated fieldbus interface.
The hydraulic axis can be driven as positioning control with digital stroke measurement (SSI interface) or by analog sensors.
Additionally, an integrated pressure limitation control function for one or two pressure sensors (differential pressure) is implemented. Command signals and actual values are transmitted by a fieldbus communication interface. Feedback are status information and actual values.
read moreProportional valves with integrated electronics (typically control valves) can be driven by the analogue output.
Internal failure and the system statuses are monitored. The ready output is available as a fieldbus information and parallel as a hardware output.
The parameterization is performed via a USB interface in combination with our PC program WPC-300. Alternatively, defined parameters can be modified via the fieldbus interface.
UHC-126-U | |||
GSD file | GSDML file | SIMATIC driver | ESI file |
CSC-151
Synchronization control module for the synchronization of two cylinders in bypass, optionally available
with power output stage
Typical applications:
- synchronization control with bypass valve
This electronic module has been developed for the control of hydraulic synchronization systems. The typical synchronization accuracy is about 0,1 % to 1 % of the sensor length (depending on the hydraulic system).
With this control concept, no absolute positions are approached, rather the synchronization of two axes is realized by a proportional directional valve arranged in bypass. A minimum of synchronization is achieved, for example via a flow divider valve or a gear divider. The proportional valve operates in parallel to compensate the specific deviation of the divider (typically 2… 10 %).
This kind of synchronization control is extremely stable and simple to use. Proportional valves with integrated electronics and external power amplifiers can be driven by the universal analog output. For valves without electronics this controller is also available with an integrated power stage.
CSC-152
Universal positioning and synchronization module, alternatively with power output stage
Typical applications:
- synchronization and positioning of two axes (up to four axes in master slave mode).
This electronic module has been developed for controlling hydraulic positioning / synchronization drives. Proportional valves with integrated or external electronics can be controlled with the universal analog output.
The internal profile generation is optimized for stroke-dependent deceleration or NC control. The controller and its settings are adapted to the typical requirements and thus offer rapid and uncritical optimization of the control behavior. The time-optimized control function offers a high degree of precision together with high stability for hydraulic drives. The movement cycle is controlled via the external position and speed inputs. The high resolution of the analog signals ensures good positioning behavior.
The synchronization control works as a second overriding velocity / position controller. Deviations between the axes will be compensated by adjusting the speed of the slave axis (or both axes in master/master mode). The speed of the axes can be limited with the external analog speed input.
Alternatively, this controller is available with an integrated power output stage.
POS-124-U
Two-axis positioning and synchronization control module with
integrated ProfiNet IO resp. Profibus DP interface and SSI sensor interface
Typical applications:
- position control and/or
- synchronization control with hydraulic axes
This electronic module has been developed for controlling two hydraulic positioning axes.
Both axes can be driven independently or controlled in synchronous mode via ProfiNet / Profibus / EtherCAT.
The differential outputs are provided for the control of proportional valves with integrated or external electronics (with differential input). Alternatively, the output can be parameterized to 4… 20 mA. This module is designed for the use with analog position sensors 0… 10 V or 4… 20 mA (scalable) as well as digital SSI sensors.
The internal status and faults information are transmitted to the master controller. Additionally, the operational readiness is reported via a READY output
Profibus | POS-124-U-PDP | GSD File | |
ProfiNet | POS-124-U-PFN | GSDML File | SIMATIC_DRIVER |
EtherCAT | POS-124-U-ETC | ESI File |
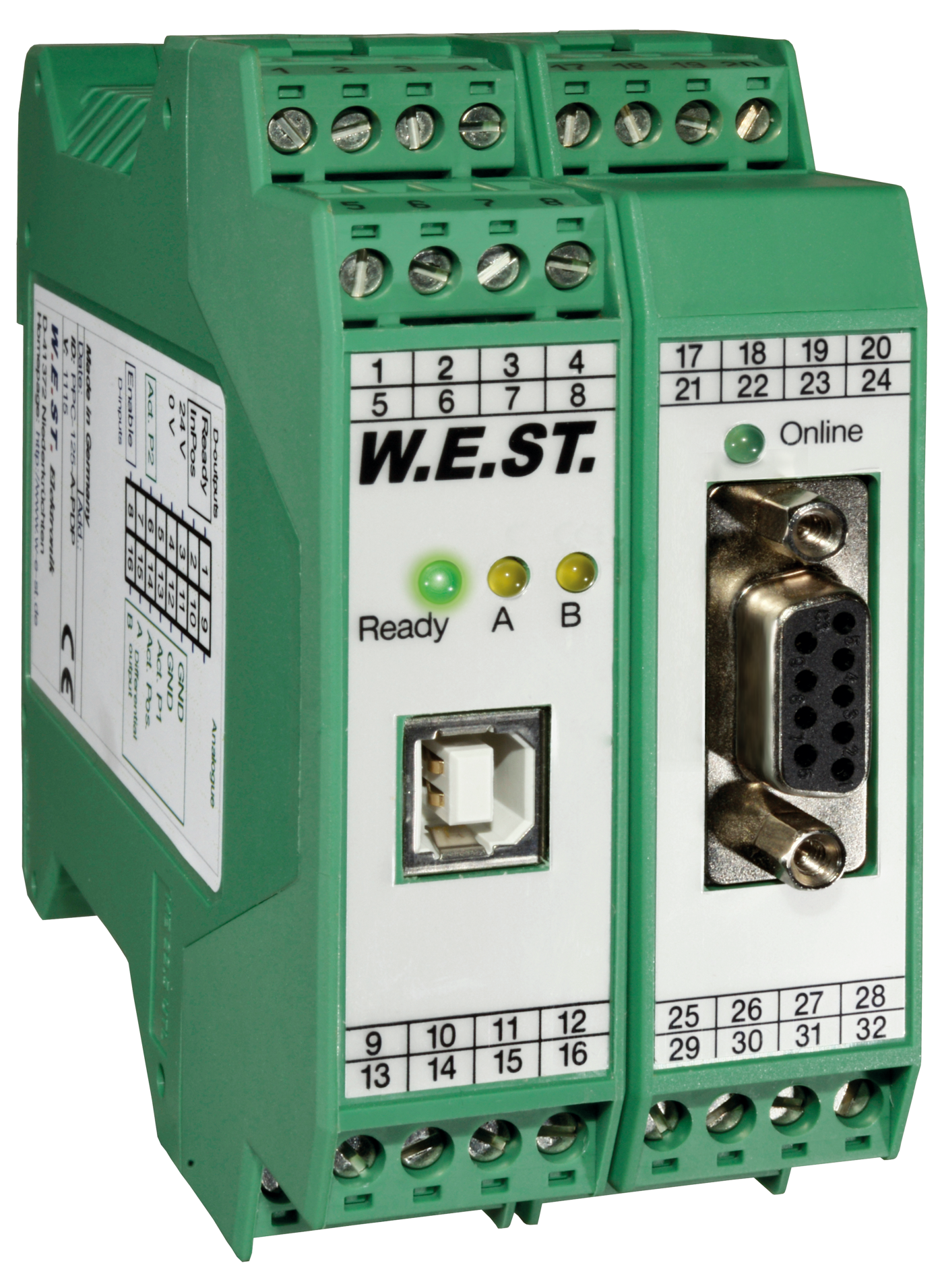
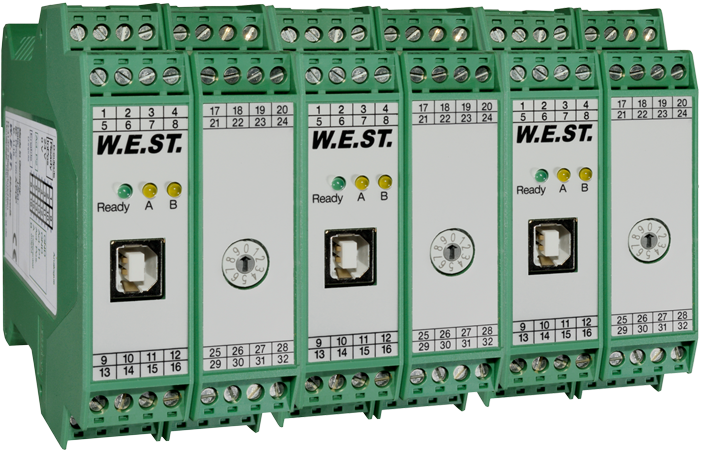
CSC-156-U-SSIC + PCK-306
Synchronization system with pressure limitation control, SSI and Profibus interface for 2 to 4 axes
Typical applications:
- positioning
- synchronization control
- pressure/force control
With a system consisting of one PCK-306 and up to four CSC-156 modules, typical synchronization applications like e.g. press and calander controls are possible. Additionally to the positioning and synchronization controller, a pressure limitation controller (differential pressure or force control) is implemented. The function can be adapted to the respective requirements via the various control bits.
Positioning: Similar to our standard positioning controller, the system can be used as point-to-point-control (stroke depended deceleration) or in NC-mode (speed controlled). By means of a few parameters, the controller gets optimized, the profile generation is set via the fieldbus (position and speed).
Synchronization control: Additionally, a superimposed synchronization control can be activated. As control structure, a PI or rather PT1 structure is used. According to the requirements, the master slave concept as well as the average determination (control of all axes to an internal calculated demand position depending on single positions and the command position) are available.
Pressure/force control: With one/two pressure sensors the force can be measured and limited. When the system switches over from synchronization control to pressure/force limitation control, the pressure limitation controller takes the priority.